九州エフ・シー・シーの強み
精密機能部品生産で培った各技術は、
より高品質・低価格へと常に進化をし続けています。
最大限活かした技術はクラッチ部品のみならず様々な部品へ活用が可能です。
接着技術
セグメント方式により様々なニーズに対応
フリクションディスク製法『セグメント方式』はF.C.C.が開発した独自製法です。クラッチ生産効率と品質の向上に飛躍的な進化をもたらした生産システムで、工程の効率化、材料歩留まりの大幅な向上を実現しています自由度の高い油溝形状が、製品に求めれる様々な要求へ対応を可能にします。
セグメント技術
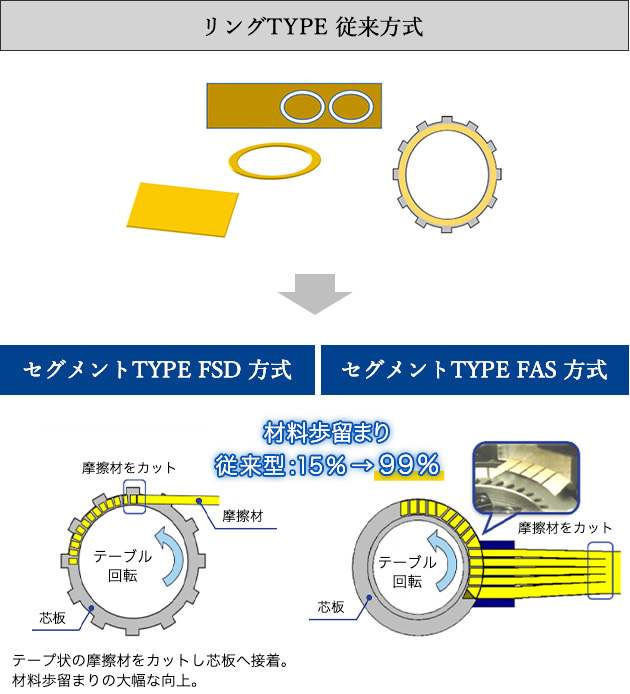
材料歩止まりが劇的に向上!
摩擦材の形状をリング型から短冊型へ、成形方法を打ち抜きからスリットへと進化させたことで、材料歩留まりを劇的に向上。大幅なコストダウンを達成します。
材料歩留まり率を従来15%から60%~100%にすることで廃棄量を大きく削減、環境にやさしいものづくりを実現します。
コア技術
進化を続けるFCCのコア技術。
多様化する顧客ニーズに応えて、姿を変えてきたFCCのセグメントディスク。
最初のセグメントディスクが生まれた1989年から今に至るまで、試行錯誤を続けてきました。初期の方式以降、要求性能に応じた溝形状のデザインや、型の隙間のけばをなくすことによるドラグトルク低減・コストダウンと、時代へのニーズに対応し、技術を進化させてきた実績があります。
アルミダイカスト技術
鋳造品質不良 ”0” を目指して
製品不良の原因となる鋳巣*1の発生を抑制するためにFCCでは真空鋳造*2や独自製法の開発で絶えず品質向上に取り組んでいます。
- *1. 鋳物内部に発生する空洞のこと
- *2. 金型内もしくは注湯系のすべてを、真空および減圧した状態で鋳造する技術
鋳巣抑制技術
金型方案
スライドコア/スクイズ金型を採用し、加工取り代ミニマム化により工数削減・鋳巣発生を抑制しています。
真空ダイカスト方案
キャビティ内を減圧して、空気や酸化膜の巻き込みを抑制します。
※製品形状により真空ブロック、チルブロック仕様見極めによる鋳巣不良抑制提案が可能
鋳造条件設定
流動解析とCTスキャナーを活用し鋳造条件を導き、内部鋳巣を削減します。
冷却システム
金型局部高温部の中子ピン冷却が可能であり、長時間連続で冷却機能を維持させ鋳造不良の削減と金型保全性向上及び金型寿命延長します。
量産システム
設計/解析/型製作までALL FCCで対応しており、短期間で見極め量産が可能です。
また鋳造から加工、検査まで一貫した生産により低コスト化、機能部品から培った技術により高精度・高品質を保証し、個別溶解炉生産により多種アルミ材料の鋳造をしています。
離型剤は回収装置にてリユースし、環境に配慮したものづくりに取り組んでいます。
プレス技術
高品質と低コストの両立化
製品形状/精度により最適製法と金型仕様から設備選定を行っております。
主なプレス製法としては打ち抜き/絞り/順送があり、プレス技術の組み合わせによりお客様のニーズに沿った製品の提供が可能です。
プレス製法
打ち抜き製法
サーボプレスのモーション設定により、製品形状に応じた最適動作を設定し加工工数削減、金型の高寿命化に繋げます。
絞り(FAD)製法
深絞りの複雑な内外歯型成形をFAD(FCC Advanced Drawing)製法により1ストロークでプレス成型し工数を短縮、コストダウンを図っています。
順送製法
複雑な形状の小物部品を順送化することで工程・工数を削減しコストダウンに繋げます。単発工程で複数の工程を必要とする製品を順送化することで金型費、生産工数を削減します。
組立技術(設備・部品)
自動車用部品の組立量産技術であらゆるニーズに対応
自動車用部品の設備組立技術(構想/設計/製造/評価)、部品組立といった量産技術を応用して、シリコンウエハー搬送装置など半導体関連の設備組立なども行っております。